Top Notch Tips About What Is MCP In Motor Control

SRM Commutation Generate Switching Sequences For Nphase Switched
MCP in Motor Control
1. What's This MCP Thing Anyway?
Ever wondered what all those acronyms mean when you're tinkering with motors or dealing with industrial automation? One that pops up frequently is MCP. Now, MCP doesn't stand for "My Cat's Pajamas" (though that would be pretty entertaining!), it's shorthand for Motor Control Panel. In motor control systems, MCP is a crucial piece of equipment. It's essentially the central hub, the brain, if you will, that manages and protects your electric motors. Think of it as the mission control for your motor operations.
The Motor Control Panel is more than just a simple switch box. It's a sophisticated assembly that houses a variety of electrical and electronic components designed to ensure motors run smoothly, efficiently, and safely. These components work together to start, stop, control, and protect the motors from potential problems, ensuring longevity and preventing costly downtime. And that, my friends, is something we all want to avoid.
So, why is the MCP so important? Imagine trying to orchestrate a complex symphony without a conductor. Chaos would ensue, right? Similarly, without a well-designed MCP, your motor system could be prone to inefficiencies, malfunctions, and even complete failures. The MCP provides the necessary control and protection to keep things running harmoniously.
Essentially, the Motor Control Panel acts as the central nervous system of your motor-driven machinery. Its where all the vital signals converge, are processed, and then sent back out to the motor, dictating its operation. Understanding the MCP and its functions is paramount for anyone working with electric motors, from seasoned engineers to budding technicians.
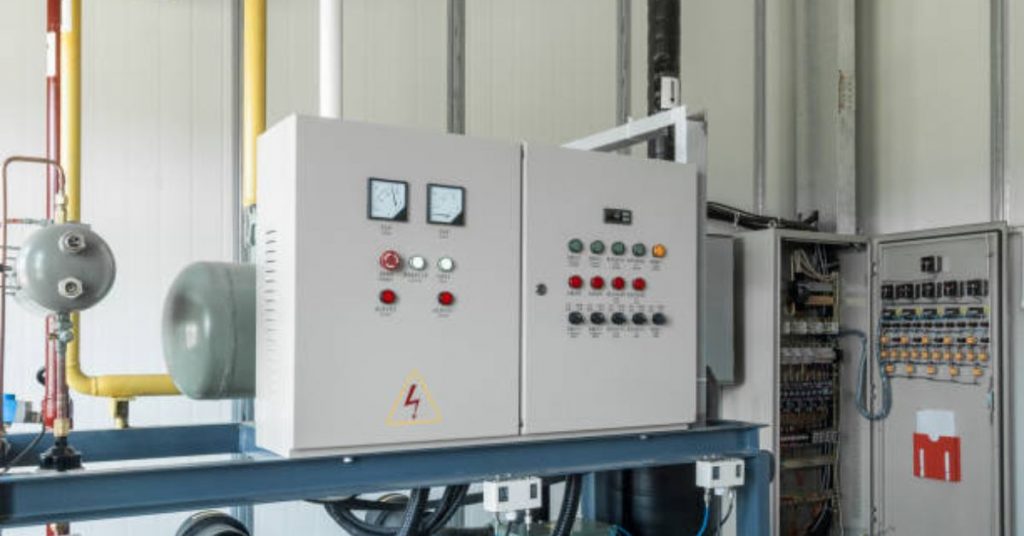
What Is A Motor Control Panel At Madalyn Hartley Blog
Why You Need an MCP
2. Protection, Control, and Peace of Mind
Now that we know what MCP stands for, let's dig into why it's so darn important. It's not just there to look pretty, although a well-organized MCP can certainly be a thing of beauty! The primary function of an MCP is to provide comprehensive protection for your motor. This includes safeguarding against overloads, short circuits, and other electrical faults that could potentially damage the motor or even cause a fire. Nobody wants that kind of excitement.
Beyond protection, the MCP also provides precise control over the motor's operation. It allows you to start, stop, and adjust the motor's speed and torque as needed. This level of control is essential for optimizing performance and ensuring that the motor is operating within its safe parameters. Think of it as having a remote control for your motor, allowing you to fine-tune its performance with ease.
Moreover, an MCP can incorporate various monitoring and diagnostic features. These features provide valuable insights into the motor's health, allowing you to identify potential problems early on and take preventative measures. This can save you significant time and money in the long run by preventing unexpected breakdowns and costly repairs. It's like having a personal physician for your motor, constantly monitoring its vital signs.
Ultimately, an MCP provides peace of mind. Knowing that your motor is protected, controlled, and monitored gives you the confidence to focus on other aspects of your operation. It's an investment in reliability and efficiency that pays dividends over time. So, next time you see an MCP, remember that it's not just a box of wires; it's a guardian angel watching over your motor.
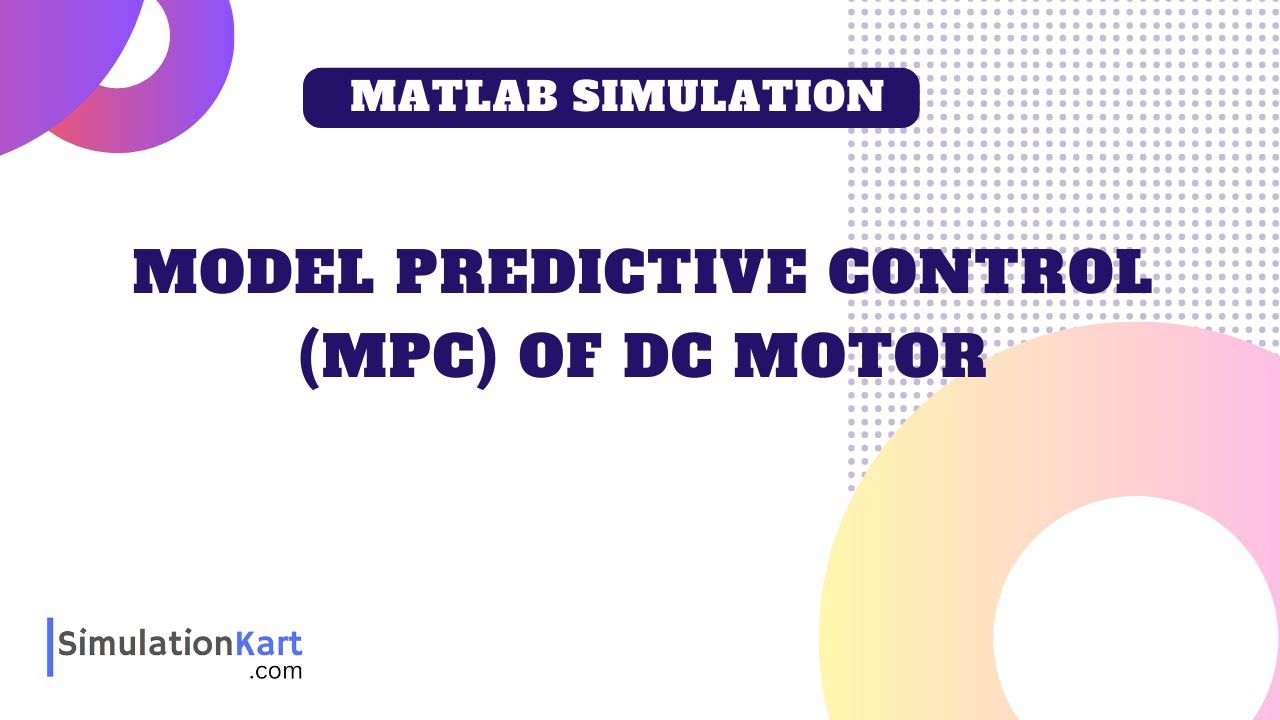
Model Predictive Control (MPC) Of DC Motor MATLAB Simulation YouTube
Key Components of a Motor Control Panel
3. The Inner Workings Explained
Let's peek inside the MCP and take a look at some of the key components that make it tick. You'll find a collection of devices working in concert to ensure the motors optimal performance and safety. These can include circuit breakers, contactors, overload relays, and various control devices. Each component plays a specific role in the overall functionality of the panel. Let's break it down.
First up are circuit breakers. These are your motor's first line of defense against overcurrents and short circuits. They're designed to trip (or break the circuit) when the current exceeds a safe level, preventing damage to the motor and other components. Think of them as electrical bouncers, keeping out the bad stuff. Next, we have contactors. These are electrically controlled switches that are used to start and stop the motor. They're typically operated by a control signal from a programmable logic controller (PLC) or other control device.
Then there are overload relays. These devices protect the motor from overheating due to excessive load. They monitor the motor's current and trip if it exceeds a predetermined threshold, preventing potential damage to the motor windings. Finally, you'll find a variety of control devices, such as pushbuttons, selector switches, and pilot lights. These devices allow operators to manually control the motor and monitor its status. Some MCPs also include advanced monitoring devices that provide real-time data on motor performance, such as voltage, current, and power consumption. These devices can be invaluable for troubleshooting and optimizing motor operation.
Understanding the function of each of these components is essential for troubleshooting and maintaining the MCP. It's like knowing the different instruments in an orchestra; each plays a vital role in creating the overall sound.

MCP Types
4. One Size Doesn't Fit All
Motor Control Panels aren't a one-size-fits-all kind of deal. Depending on the application and the motor's requirements, you'll find different types of MCPs designed to meet specific needs. These range from simple, manually operated panels to sophisticated, fully automated systems. Let's explore a few common types.
First, there are manual motor starters. These are the simplest type of MCP, typically used for small motors where manual control is sufficient. They consist of a basic switch or circuit breaker that allows the operator to manually start and stop the motor. No frills, just basic functionality. Then, we have magnetic motor starters. These are more sophisticated than manual starters and use a magnetic contactor to start and stop the motor. They offer improved protection and control compared to manual starters and are commonly used for medium-sized motors.
For more complex applications, you'll find variable frequency drives (VFDs) incorporated into the MCP. VFDs allow you to adjust the motor's speed and torque, providing precise control over its operation. This is particularly useful for applications where the motor's load varies, such as pumps and fans. The ultimate in MCP sophistication comes in the form of programmable logic controllers (PLCs). These are used to automate motor control and integrate it with other systems. PLCs can be programmed to perform a wide range of tasks, such as starting and stopping motors based on pre-defined conditions, monitoring motor performance, and providing alarms in case of faults. They're the brains of the operation.
The choice of MCP type depends on several factors, including the motor's size, the application's requirements, and the level of automation desired. Understanding the different types of MCPs available is essential for selecting the right one for your specific needs.

Troubleshooting Common MCP Issues
5. When Things Go Wrong (and How to Fix Them)
Even the best-designed MCPs can experience problems from time to time. Whether it's a tripped circuit breaker or a malfunctioning contactor, knowing how to troubleshoot common MCP issues can save you time and money. However, it is very important to turn the MCP off before attempting to troubleshoot it! Safety first.
One common problem is a tripped circuit breaker. This could be caused by an overload, a short circuit, or a faulty component. Start by checking the motor's load to ensure that it's not exceeding its rated capacity. If the load is within acceptable limits, inspect the wiring for any signs of damage or shorts. If you can't find any obvious problems, try resetting the circuit breaker. If it trips again immediately, there's likely a more serious problem that requires further investigation. Another common issue is a malfunctioning contactor. This can prevent the motor from starting or stopping correctly. Check the contactor's coils and contacts for signs of damage or wear. If the contactor is not functioning properly, it may need to be replaced.
Sometimes, the problem lies with the overload relay. This can trip even when the motor is not overloaded if the relay is faulty or improperly calibrated. Check the relay's settings and ensure that they are appropriate for the motor's current rating. If the relay continues to trip, it may need to be replaced. Finally, don't forget to check the wiring. Loose or corroded connections can cause a variety of problems, including voltage drops and intermittent faults. Inspect all connections and tighten or clean them as needed. Also make sure to check the voltage coming into the MCP and that it is within the safe range for the components being used in the MCP.
Remember, working with electrical equipment can be dangerous. If you're not comfortable troubleshooting MCP issues yourself, it's always best to call a qualified electrician. A little caution can go a long way in preventing accidents and ensuring your safety. If you do decide to troubleshoot it yourself, be sure to have someone present with you!
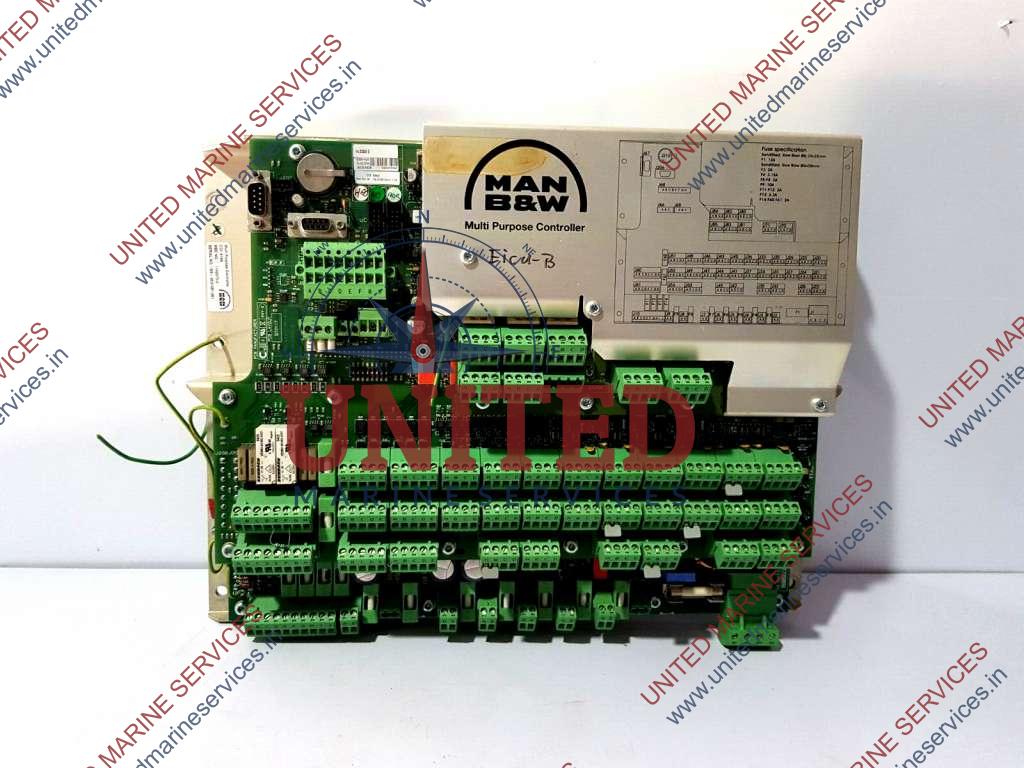
MAN B&W MULTI PURPOSE CONTROLLER 11420752 United Marine Services
FAQ
6. Because Curiosity Didn't Actually Kill the Cat
Still have some lingering questions about MCPs? Fear not! Here are some frequently asked questions to help you further demystify this essential component of motor control systems.
Q: What's the difference between an MCC and an MCP?
A: Good question! An MCC (Motor Control Center) is essentially a larger version of an MCP, typically housing multiple MCPs in a single enclosure. Think of an MCP as a single apartment, and an MCC as the entire apartment building. MCCs are generally used in larger industrial facilities where multiple motors need to be controlled from a central location.Q: Can I build my own MCP?
A: While it's technically possible to build your own MCP, it's generally not recommended unless you have extensive electrical knowledge and experience. Building an MCP requires a thorough understanding of electrical codes and safety standards. Furthermore, a poorly designed or constructed MCP can be dangerous and may not provide adequate protection for your motor. It's usually best to purchase a pre-built MCP from a reputable manufacturer.Q: How often should I inspect my MCP?
A: The frequency of MCP inspections depends on the application and the operating environment. In general, it's a good idea to perform a visual inspection of the MCP at least once a month. This includes checking for loose connections, signs of corrosion, and any other visible damage. A more thorough inspection, including testing of the components, should be performed at least once a year by a qualified electrician.Q: What are some signs that my MCP is failing?
A: Signs of a failing MCP can include tripped circuit breakers, malfunctioning contactors, unusual noises, and visible damage. If you notice any of these symptoms, it's important to investigate the problem promptly to prevent further damage to the motor or other equipment. If you're unsure about what to do, it's always best to consult with a qualified electrician.